Insights Into In-Office Milling Technology
The ability to create crowns and other restorations in-office and reduce dependence on dental laboratories has many dentists considering adding in-office milling to their practice offerings.
The ability to create crowns and other restorations in-office and reduce dependence on dental laboratories has many dentists considering adding in-office milling to their practice offerings. But beyond the clinical and marketing advantages — as well as obvious patient benefits — of “same-day” dentistry, clinicians should consider how bringing fabrication in-house can elevate their level of care.
When thinking of adding in-office milling, author, lecturer and educator Robert W. Berg, DMD, who practices prosthodontics in New York City, recommends doing more than an ROI analysis. “It’s not simply a question of how quickly you can pay off the debt on the mill before making a profit,” he explains. “You should also be thinking of how you can leverage this technology to transform and facilitate care.” Berg likewise advises dentists to evaluate the applications the technology will be used for.
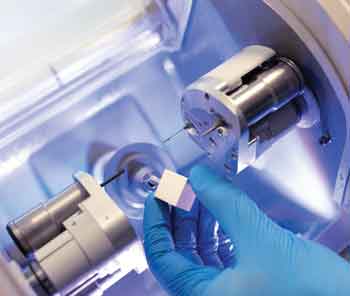
Noting the variety of restorations suitable for in-office milling, Amit Punj, BDS, DMD, MCR, FACP, a clinician as well as chief and residency program director of prosthodontics at New York’s Montefiore Medical Center, says, “Most indirect, single-unit restorations, such as inlays, onlays, veneers and crowns, as well as implant restorations, can be manufactured using ceramics, composites and acrylic resins. Depending on the office’s capabilities and interest, multiple units and three-unit fixed partial dentures can be fabricated in-house, as well.”
However, this technology does have its limitations. According to Punj, restorations that require the use of feldspathic ceramic, frameworks for removable partial dentures, large-span metal alloys frameworks, overdenture bars, as well as complete-arch high strength 3Y zirconia prostheses are better managed by a dental lab.
Besides considering how patients and practices will benefit from investing in this technology, the time and resources needed to design and fabricate restorations should also be taken into account. “The current programs used to design and process restorations are intuitive, smart, and require minimal to no editing for most single-unit restorations,” Punj explains. Berg expands on the thought, saying, “Once you are familiar with the software, the single-unit design process takes about five minutes. With artificial intelligence built into today’s software, less time is spent identifying the margin and auto generating a crown design. Rather, most of the time is used for altering or adding a personal touch to the restoration.”
Once staff gets past the learning curve and is familiar with the design and fabrication process, the productivity, efficiency, patient satisfaction, and time saved is unparalleled, notes Punj. “In-office milling units these days are efficient, reliable, have a smaller footprint, and can even mill zirconia, which was not possible until a few years ago,” he adds.
In terms of the milling process, Berg explains that fabrication needs little hands-on supervision once the milling machine is set up and the dental team is familiar with the design software. That said, dentists must still be prepared to train staff, maintain the unit, and stay on top of software updates.
Berg offers some final advice to ensure this technology is successfully incorporated into practice. “Foremost, you must fully buy into the process,” he says. “Once you have established workflow protocols and designated team responsibilities, in-office milling becomes a seamless process very quickly.”
From Decisions in Dentistry. August 2021;7(8)46.