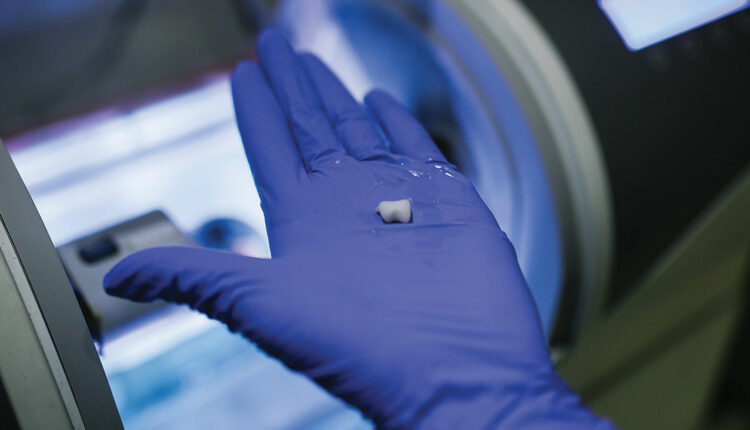
Byte into the Future With Milling Machines
Milling machines play a vital role in modern digital dentistry. During my tenure as a dental lab technician, we used them to streamline our lab production, but their use in chairside manufacturing has deepened my interest in their potential. As a recent graduate of prosthodontics, I appreciate the differences between in-office and remote lab milling workflows. Choosing between the two necessitates a meticulous and objective consideration of patient-specific factors, material limitations, temporal efficiency, and cost.
Digital workflows include data acquisition, computer-aided design (CAD), and computer-aided manufacturing (CAM). For in-office milling, data acquisition requires an intraoral scanner, chairside design, in-house milling, post-processing modification, and delivery within a few hours. In contrast, remote lab milling requires only data acquisition (analog or digital) in the office, while the remaining tasks — CAD/CAM procedures, milling, and post-processing — are accomplished by the lab within a few weeks. These distinct workflows have varied indications based on specific procedural goals.
Proper case selection is particularly important for in-house milling. The proposed abutments must be scannable with shallow, well-retracted finish lines.1 In the absence of physical casts, the number and position of the teeth can greatly impact the complexity and predictability of treatment. Cases involving the esthetic zone, multiple teeth, or significant malocclusion may be better suited for lab milling workflow to take advantage of a technician’s expertise.
Material selection is also a key consideration. Lithium disilicate is a proven restorative material for chairside milling, but composite resin and zirconia are growing in popularity.2 However, their use requires workflow modifications that may be accommodated by off-site milling. For example, while chairside zirconia can be sintered in as little as 19 minutes, thicker zirconia restorations may not be amenable to expedited sintering cycles as they alter the translucency, resulting in compromised esthetics.3 Although most post-processing procedures can be done in-house, materials that require complex, intricate, or lengthy treatment can be best managed with remote lab fabrication.2
Both milling workflows have evolved due to demand for more streamlined efficient fabrication methods. While both workflows take about the same amount of chair time, the time efficiency differs.4 In-office milling can be completed in a single visit, eliminating the need for temporization and a separate insertion appointment. However, processing time, additional staff training for delegated procedures, and varying degrees of provider involvement must be considered. Conversely, remote lab milling involves two shorter appointments but requires fabrication of a provisional and second appointment for insertion. Therefore, the preferred approach is left to the provider and patient.
The initial financial investment for in-office milling is substantial. It requires a mill, employee training, inventory management, software updates, and routine maintenance — a total investment often more than $100,000.2 The time required to recoup this sizeable expenditure can be as brief as a few years but depends heavily on the office overhead, workflow efficiency, and the number of units fabricated in a given period. On the other hand, lab milling mitigates these upfront expenses.
Taken together, the decision to proceed with a specific workflow depends on patient desires, material selection, clinical efficiency, and economic impact. While a one-size-fits-all solution remains elusive, careful deliberation can lead to a well-informed decision about integrating either workflow in a busy practice.
References
- Ferrari Cagidiaco E, Zarone F, Discepoli N, Joda T, Ferrari M. Analysis of the reproducibility of subgingival vertical margins using intraoral optical scanning: a randomized controlled pilot trial. J Clin Med. 2021;10:941.
- Blatz MB, Conejo J. The current state of chairside digital dentistry and materials. Dent Clin North Am. 2019;63:175-197.
- Al-Haj Husain N, Özcan M, Dydyk N, Joda T. Conventional, speed sintering and high-speed sintering of zirconia: a systematic review of the current status of applications in dentistry with a focus on precision, mechanical and optical parameters. J Clin Med. 2022;11:4892.
- Stromeyer S, Wiedemeier D, Mehl A, Ender A. Time efficiency of digitally and conventionally produced single-unit restorations. Dent J (Basel). 2021;9:62.
From Decisions in Dentistry. April/May 2024; 10(3):14